DIY Wound Packing Trainers
DIY wound packing trainers are not hard to make, are great training materials for a stop the bleed-style class, and depending on how many you make, can cost around $8-15 each.
These are not terribly hard to make, and are great training materials for a stop the bleed-style class.
Steps
1. 3D print some molds using files downloaded from: https://www.decentsimulators.com/miniwoundpackingtrainers
2. Following the instructions provided by Smooth-On (they're genuinely very good), mix up ~300mL of Ecoflex 00-30 (https://www.smooth-on.com/products/ecoflex-00-30/) with some Silc Pig (https://www.smooth-on.com/products/silc-pig/) and pour it into the mold. Use very little Silc Pig - drizzle in MAYBE a milliliter, stir a bit, and see how it looks. You hardly need any at all, and more than 3% by weight can apparently cause problems with the casting.
3. Let it cure, peel the trainer carefully from the printed mold, and you're done. Yep, that's literally it. You can start over from step number one and re-use the same molds.
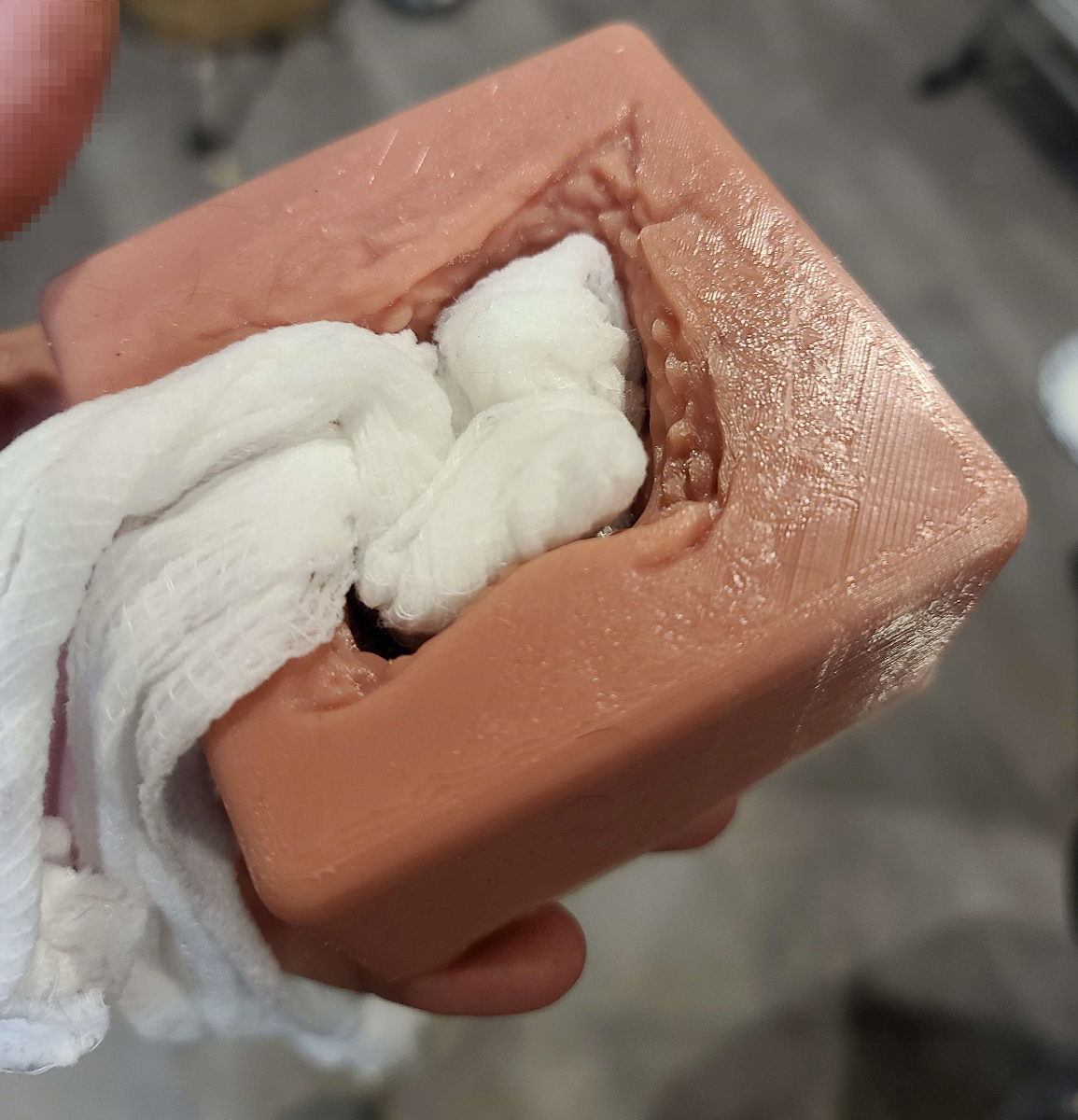
Bill of Materials
These materials will allow you to make roughly 4-5 trainers. After that, you're only limited by the Ecoflex - the molds can be re-used effectively infinitely, and you use so little Silc Pig that I expect you could make hundreds of trainers before you ran out. After the setup costs, and if you don't buy in bulk, you're probably looking at roughly $8-10 per trainer in material costs, worst-case.
Item | Link | Price |
---|---|---|
3D Printed Molds | https://www.decentsimulators.com/miniwoundpackingtrainers | $10 |
Ecoflex 00-30 | https://www.smooth-on.com/products/ecoflex-00-30/ | $36 |
Silc Pig | https://www.smooth-on.com/products/silc-pig/ | $27 |
Total | $73 |
Optional For Extra Realism
If you want, you can use Slacker (https://www.smooth-on.com/products/slacker/) to give a more flesh-like feel. The extra difficulty here is that Slacker makes the material sticky, which is... weird, and can make packing hard. To fix this, you have to mix up a small amount of Ecoflex and pour a thin layer over the whole mold, let it cure (or at least mostly set up) and then fill the rest with your Ecoflex + Slacker mixture. This ensures a thin layer of not-sticky material on the outside of the finished product, with an accurate-feeling mass of material inside it.
In my experience, a mix of about 30 grams of Slacker for 50 grams of Part B Ecoflex 00-30 (and then the other 50 grams Part A) is about right for a good feel.